國內(nèi)外汽車制造和使用環(huán)境的不斷變化,對汽車車身的開發(fā)提出了更高的要求。盡管受到投資成本、工藝可靠性等因素的困擾,國內(nèi)一些中小企業(yè)還把優(yōu)化現(xiàn)有生產(chǎn)工藝作為企業(yè)發(fā)展的首選,本文興迪源機械帶來分享 | 汽車沖壓成形新工藝。
一、新工藝:
國內(nèi)外汽車制造和使用環(huán)境的不斷變化,對汽車車身的開發(fā)提出了更高的要求。盡管受到投資成本、工藝可靠性等因素的困擾,國內(nèi)一些中小企業(yè)還把優(yōu)化現(xiàn)有生產(chǎn)工藝作為企業(yè)發(fā)展的首選,但在國外以及國內(nèi)的一些大型企業(yè)中已開始廣泛研究和開發(fā)板料成形新技術(shù)、新工藝,如內(nèi)高壓成形、液壓拉深、熱成形和旋轉(zhuǎn)落料等。采用新工藝有很多技術(shù)上的優(yōu)勢,可以提高材料利用率,減少零件制造工序,降低生產(chǎn)成本。
二、液壓拉深技術(shù):
拉深成形廣泛應(yīng)用于航空航天、汽車和電子等領(lǐng)域,傳統(tǒng)的拉深模由剛性凸模、壓邊圈和凹模構(gòu)成,拉深過程中,凸模底部材料幾乎不發(fā)生塑性變形,坯料的主要變形區(qū)是凸緣區(qū)。該區(qū)域材料在周向壓應(yīng)力和徑向拉應(yīng)力作用下發(fā)生塑性變形并被逐漸拉入凹模內(nèi)轉(zhuǎn)化形成筒壁。液壓拉深技術(shù)是在原理和方法上不同于傳統(tǒng)拉深方法的一種新技術(shù),它包括液壓深拉深和液壓正拉深2種。
2.1傳統(tǒng)剛性拉深模的局限性
在傳統(tǒng)的拉深過程中,極限拉深系數(shù)主要受到筒壁傳遞拉應(yīng)力能力的限制,拉深時筒壁所受拉應(yīng)力超過極限拉應(yīng)力時,將產(chǎn)生拉裂現(xiàn)象。此外,傳統(tǒng)的剛性拉深工藝在減少拉深工序,降低模具成本,提高拉深件尺寸精度和表面粗糙度以及適應(yīng)多品種小批量生產(chǎn)等方面受到一定限制,而液壓拉深技術(shù)在這些方面則表現(xiàn)出較明顯的優(yōu)勢。
2.2液壓深拉深
2.2.1液壓深拉深原理
液壓深拉深是利用壓力介質(zhì)進行成形,主要應(yīng)用在雙動液壓機上,液體介質(zhì)一般為油或水。
2.2.2液壓深拉深模具結(jié)構(gòu)
液壓深拉深模在下模設(shè)置壓力介質(zhì)容器作為液壓腔,并用于緊固凹模。液壓容器與壓機的壓力調(diào)節(jié)裝置相連,用一個夾緊環(huán)將凹模固定在液壓容器上,同時環(huán)上開有槽。可將泄漏的液體排放出去。上模則由拉深凸模和壓邊圈構(gòu)成,壓邊圈上裝有1個濺油環(huán),用來收集泄漏的液體。液壓深拉深模具結(jié)構(gòu)如圖1所示。
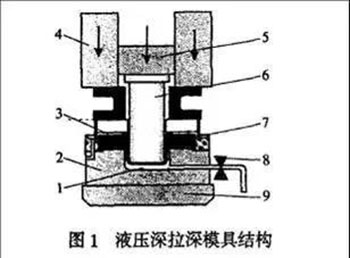
2.2.3液壓深拉深成形方法
液壓深拉深成形方法主要包括:機械液壓拉深法、動態(tài)機械液壓拉深法和徑向加壓機械液壓拉深法。在基本狀態(tài)下壓機是打開的,液壓容器內(nèi)充滿液體。坯料放在凹模上后壓機閉合,壓邊圈壓緊坯料。開始成形。拉深凸模進入液壓容器,液壓容器內(nèi)液體產(chǎn)生壓力。成形過程中板料始終緊壓在凸模上。由與液壓容器相連的調(diào)節(jié)系統(tǒng)根據(jù)工件不同拉深深度調(diào)節(jié)液壓容器內(nèi)的壓力。
2.2.4液壓深拉深成形的優(yōu)點
成形過程中拉深凸模通過壓入液壓容器產(chǎn)生向各個方向作用的壓力,并將要成形的坯料始終緊壓在凸模表面,加大了凸模與坯料之間的附著摩擦。使拉深力大為提高,而且成形件精度較高,還有利于減少回彈。此外。由于板料不是在剛性圓角上進行拉深。而是被通過間隙的液體壓力拉深,因而成形件應(yīng)力分布均勻。表面質(zhì)量高。同時,因為成形工序減少。使模具費用減少,成本降低。
2.3液壓正拉深
汽車上的大面積構(gòu)件,如車蓋、車門或發(fā)動機罩等。按其造型在構(gòu)件中部抗翹曲強度很小,原因是構(gòu)件中部變形程度小,材料達(dá)不到足夠的強化處理,當(dāng)覆蓋件承受很小的外力時就會發(fā)生變形,因此構(gòu)件的穩(wěn)固性低。會對汽車的碰撞行為和抗沖擊強度產(chǎn)生不良影響。液壓正拉深方法是一種既可以解決上述問題又可以降低模具費用的成形工藝。
2.3.1液壓正拉深原理與模具結(jié)構(gòu)
液壓深拉深是利用壓力介質(zhì)(大多是油水乳劑)進行成形。拉深過程中,大面積板坯借助液壓四周緊密地壓緊在凹模和壓邊圈(這里以液壓容器的形式出現(xiàn))之間。液壓乳劑通過一個增壓器充入液壓容器中。并形成一定的壓力,這時板坯有控制地向上鼓起。并且在最終成形構(gòu)件的整個面上進行預(yù)拉深,直到工件的中間面積貼到凸模上。預(yù)拉深后,壓邊圈、板坯和凹模構(gòu)成的整體壓向凸模,此過程中液壓乳劑被擠壓。壓力可以保持不變、遞增或者遞減的形式調(diào)整,拉深過程結(jié)束后,液壓乳劑的壓力重新產(chǎn)生,使板坯緊壓在凸模上達(dá)到理想的形狀。模具結(jié)構(gòu)見圖2。
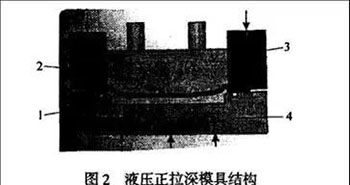
2.3.2液壓正拉深的優(yōu)點
由于板坯不與凸模或者凹模摩擦,而是通過液壓乳劑將板坯擠壓到凸模上,不僅模具磨損小,耐用度高。而且工件可達(dá)到較理想的表面質(zhì)量。此外,由于使用液壓正拉深工藝費用低于傳統(tǒng)工藝。用1副模具可以加工各種材料(鋼、鋁)和任何厚度的板料,而且通常可以節(jié)省一個加工工序,模具費用大為降低。
三、管狀內(nèi)高壓成形技術(shù):
內(nèi)高壓成形技術(shù)在加工幾何形狀復(fù)雜的空心件方面具有明顯的技術(shù)和經(jīng)濟優(yōu)勢。20世紀(jì)90年代中期,管狀內(nèi)高壓成形技術(shù)開始應(yīng)用于汽車領(lǐng)域,目前在歐洲、美國和韓國汽車制造業(yè)已經(jīng)得到很好的應(yīng)用。
3.1內(nèi)高壓成形工藝相對于傳統(tǒng)工藝的優(yōu)勢
以汽車上的排氣管為例,傳統(tǒng)排氣管的制造方法有2種:一是采用整體鑄造件,由于采用的是鑄造工藝,因而不僅尺寸精度無法保證,而且零件表面質(zhì)量很差;二是采用薄鋼管成形,即將幾根鋼管單獨成形,然后將其焊接在一起,缺點是零件多、成本高,且整個排氣系統(tǒng)焊縫多。
運用內(nèi)高壓成形技術(shù)不僅能制作幾何形狀復(fù)雜的構(gòu)件,零件重量輕,而且加工的零件是整體,不僅沒有焊縫,可以減少腐蝕,而且成形零件精度高;此外,由于冷作硬化能提高成形零件的剛性,零件在發(fā)生碰撞時更有優(yōu)勢。
3.2管狀內(nèi)高壓成形原理及模具結(jié)構(gòu)
內(nèi)高壓成形技術(shù)是一種冷成形工藝,可用來加工管坯等尺寸形狀復(fù)雜的空心件。在密閉的模具內(nèi)通過水壓從管子內(nèi)側(cè)使金屬管膨脹。模具由上、下模組成。通過壓機行程以及油缸托架高度決定裝模高度,依據(jù)行程或壓力可調(diào)節(jié)軸向缸調(diào)節(jié)密封壓頭使管坯密封,然后進一步推動管坯兩端使其鐓粗。模具結(jié)構(gòu)示意圖見圖3。
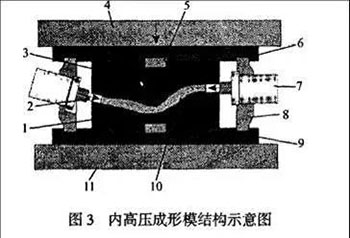
3.3內(nèi)高壓成形的特點及主要應(yīng)用領(lǐng)域
內(nèi)高壓成形坯料一般采用半成品,如拉拔管、焊接管、雙層管或者擠壓型材、預(yù)成形板坯等斷面為圓形的管坯。生產(chǎn)中如果工件由于其幾何形狀或者特殊要求而不能被脹形到最終尺寸,還需對工件進行切割、沖壓或者銑削加工。
在實際應(yīng)用方面,內(nèi)高壓成形工藝以其結(jié)構(gòu)和設(shè)計的多樣性成功地應(yīng)用在生產(chǎn)強度高、壽命長、重量輕的零部件上,如汽車排氣管(見圖4)、前、后懸掛、底盤和結(jié)構(gòu)零件等。目前,歐寶Corsa的發(fā)動機支架、BMW儀表盤支撐梁以及大眾公司某汽油發(fā)動機排氣管制造都采用內(nèi)高壓成形技術(shù)。
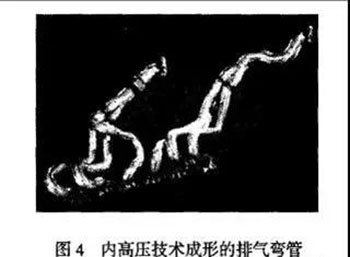
四、熱成形技術(shù):
4.1采用熱成形技術(shù)的優(yōu)越性
熱成形技術(shù)最早應(yīng)用于航天、航空等領(lǐng)域,近些年來,為減輕零部件重量,提高車身防撞能力,大量新材料也開始應(yīng)用到汽車制造中。這些新材料強度高、性能優(yōu)越,但有一個共同的特點,那就是在常溫下,材料的塑性變形范圍很窄,所需成形力大、易開裂,回彈嚴(yán)重且成形困難,但在高溫條件下就大不相同。例如,鈦合金鈑金件只有在一定的高溫(550~750℃)下,其成形性能才能充分發(fā)揮;應(yīng)用熱成形工藝加工硼合金鋼不僅可以大幅提高材料可成形性,降低成形力,而且成形零件強度、精度高,回彈小,特別適合生產(chǎn)超高強度防撞梁和B柱加強板。目前廣泛采用熱成形工藝的材料包括硼合金鋼、鈦合金、鎂合金等。
4.2熱成形的特點
在熱成形過程中,由于熱應(yīng)力的存在,材料極易產(chǎn)生裂紋,通常可以采用通過增加工序,將總變形量化小分解到各成形工序的方法加以解決;起皺可以在增加工序的基礎(chǔ)上,通過過渡結(jié)構(gòu)來消除。但是增加工序不僅要增加模具數(shù)量,而且每道工序后坯料表面會因氧化和溫度不均等原因使模具滑動面之間極易卡死,故熱成形模具結(jié)構(gòu)應(yīng)盡可能簡單。
4.3熱成形工藝的缺點
熱成形工藝作為一種新型、特殊工藝也有其自身的缺點。除了熱成形零件后續(xù)加工難度大,熱成形工序并入現(xiàn)有沖壓車間困難外,與普通金屬模具相比,由于受模具材料強度選擇、熱處理工藝制定方法、高應(yīng)力集中、模具表面溫度頻繁升高和降低以及模具型腔表面高溫軟化加劇磨損等因素的影響,熱成形模具經(jīng)常會出現(xiàn)塑性變形失效、疲勞失效和冷熱疲勞失效等問題,降低了模具使用壽命。
五、結(jié)束語:
對于汽車沖壓件制造企業(yè)來說,雖然在汽車沖壓件成形過程中采用新技術(shù)和新工藝存在投資大、新技術(shù)不夠成熟等風(fēng)險,但只有掌握了新技術(shù)、新工藝才有可能更大程度地降低成本和提高勞動生產(chǎn)率,才有可能在市場競爭中覓得先機,不斷地開發(fā)和采用新技術(shù)、新工藝代表著汽車制造業(yè)的發(fā)展方向和未來。
【興迪源機械簡介】
興迪源機械(Xingdi Machinery)是一家專注流體壓力成形技術(shù)的鍛壓設(shè)備制造企業(yè)。自2007年創(chuàng)立以來,興迪源機械一直致力于內(nèi)高壓成形的技術(shù)創(chuàng)新和產(chǎn)品研發(fā)。主營產(chǎn)品范圍從生產(chǎn)普通液壓設(shè)備,現(xiàn)今發(fā)展至生產(chǎn)、研發(fā)國內(nèi)頂尖流體壓力成形技術(shù)的鍛壓設(shè)備。
目前,興迪源內(nèi)高壓成形智能設(shè)備已運用在制造航空、航天、核電、石化、汽車、摩托車、自行車業(yè)的沿構(gòu)件軸線變化的圓形、矩形或異形截面空心構(gòu)件以及管路配件的生產(chǎn)制造中。同時也適用于生產(chǎn)航空飛行器上輕體構(gòu)件有空心結(jié)構(gòu)框架、發(fā)動機上中空軸類件、進排氣系統(tǒng)異型管和復(fù)雜管件等。