液壓成形( Hydroforming)是指利用液體作為傳力介質或模具使工件成形的一種塑性加工技術,也稱為液力成形。本文興迪源機械帶來液壓成形技術的分類、成形原理及特點。
一、液壓成形技術的分類:
液壓成形( Hydroforming)按使用的液體介質不同,可將液壓成形分為水壓成形和油壓成形。水壓成形使用的介質為純水或由水添加一定比例的乳化油組成的乳化液;油壓成形使用的介質為液壓傳動油或機油。
液壓成形( Hydroforming)按使用的液體介質不同,可將液壓成形分為水壓成形和油壓成形。水壓成形使用的介質為純水或由水添加一定比例的乳化油組成的乳化液;油壓成形使用的介質為液壓傳動油或機油。
按使用的坯料不同,液壓成形分為三種類型:管材液壓成形( Tube Hydroforming)、板料液壓成形( Sheet Hydroforming)、殼體液壓成形( Shell Hydroforming)。板料和殼體液壓成形使用的成形壓力較低,管材液壓成形使用的壓力較高,又稱為內高壓成形( Internal High Pressure Forming)。
板料液壓成形使用的介質多為液壓油,最大成形壓力一般不超過100MPa。殼體液壓成形使用的介質為純水, 最大成形壓力一般不超過50MPa。管材液壓成形使用的介質多為乳化液, 其成形壓力較高,工業生產中使用的最大成形壓力一般不超過400MPa。
二、管材液壓成形的原理及特點:
管材液壓成形是以管材作坯料,通過管材內部施加高壓液體和軸向補料把管材壓入模具型腔使其成形為所需形狀的工件,成形原理如圖3.1所示。由于使用乳化液(在水中添加少量的防腐劑等組成)作為傳力介質,因此稱為管材液壓成形或液壓成形。
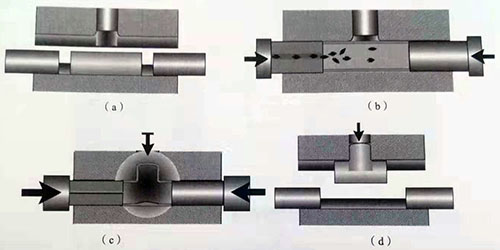
圖3.1管材液壓成形原理
(a)模具閉合;(b)快速充液;(c)液壓成形;(d)開啟模具
按成形零件的種類,管材液壓成形分為三類:①變徑管液壓成形。②彎曲軸線構件液壓成形。③多通管液壓成形。
變徑管是指管件中間一處或幾處的管徑或周長大于兩端管徑。其成形工藝過程可以分為三個階段。初始充填階段,模具閉合后,將管的兩端用水平沖頭密封,使管坯內充滿液體,并排出氣體,實現管端沖頭密封;成形階段,對管內液體加壓脹形的同時,兩端的沖頭按照設定的加載曲線向內推進補料,在內 和軸向補料的聯合作用下使管坯基本貼靠模具,這時除了過渡區圓角以外的大部分區城已經成形;整形階段,提高壓力使過渡區圓角完全貼靠模具而成形為所需的工件。
對于彎曲軸線異型截面管件的液壓成形工藝包括:彎曲、預成形、液壓成形等主要工序。有時液壓成形也與液壓沖孔工序結合,在成形后的液壓支撐下直接沖孔。
多通管件的種類較多,按照多通數量分為直三通管(T形管)、斜三通管(Y形管)、U形三通管、X形四通管和五通以上的多通管。按主管、支管直徑大小分為等徑和異徑多通管;按軸線形狀,分為直線和曲線多通管;按對稱性,分為對稱和非對稱多通管。按照壁厚大小,分為厚壁和薄壁多通管,薄壁一般指0.5-2mm的管件。T形和Y形三通管件是多通管中應用最多的結構形式。
三、板料液壓成形的原理及特點:
板料液壓成形是利用液體作為傳力介質來傳遞載荷,使板料成形到具上的一種板料成形方法,成形原理如圖3.2所示。根據液體凸模可將之進一步分類為充液拉深成形和液體凸模拉深成形。
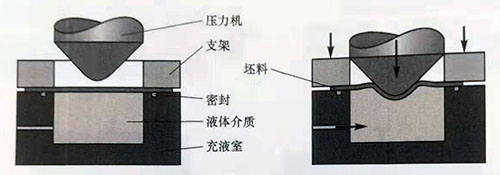
圖3.2板料液壓成形原理
1.充液拉深(用液體介質代替凹模)
成形工藝:板材充液拉深成形工藝可分為四個階段,第一階段,首先開動液壓泵將液體介質充滿充液室至凹模表面,在凹模上放好坯料;第二階段,施加壓力;第三階段,凸模開始壓入凹模,自然增壓或者通過液壓系統使充液室的液體介質建立起壓力,將板件緊緊壓貼在凸模上;第四階段,同時液體沿法蘭下表面向外流出,形成液體潤滑。
2.液體凸模拉深(以液體介質作為凸模)
液體凸模拉深成形則是以液體介質代替凸模傳遞載荷,液壓作為主驅動力使坯料變形,還料法蘭區逐漸流入凹模,最終在高壓作用下使坯料貼靠凹模型腔,零件形狀尺寸靠凹模來保證。這一成形法通過合理控制壓邊力可使還料產生拉一脹成形,應變硬化可提高曲面薄殼零件的剛性、壓曲抗力和抗沖擊能力。因此,它非常適于鋁合金和高強鋼等輕合金板料形狀復雜(特別是局部帶有小圓角)、深度較淺的零件成形。
板材液壓成形優點:提高成形極限和減少成形道次。缺點:①由于充液需要時間,生產效率低。②設備噸位大。
四、殼體液壓成形的原理及特點:
殼體液壓成形是采用一定形狀的封閉多面殼體作為預成形坯,在封閉多面殼體充滿液體后,通過液體介質在封閉多面殼體內加壓,在內壓作用下殼體產生塑性變形而逐漸趨向于最終的殼體形狀,如圖3.3所示。最終殼體形狀可以是球形、橢圓、環殼等。其成形工藝:先由平板經過焊接形成封閉多面殼體, 然后在封閉多面體內充滿液體介質(一般為水),并通過一定加壓系統施加壓力,在內壓作用下殼體產生塑性變形而逐漸趨向于球殼。
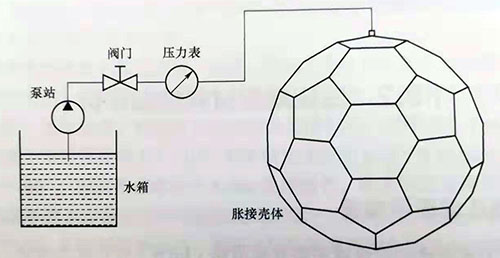
圖3.3殼體液壓成形原理
殼體液壓成形優點:
①不需要模具和壓力機,產品初期投資少,因而可降成本,縮短生產周期。
②容易變更殼體壁厚和直徑。
③與傳統的先成形后焊接工藝相比,由于焊接變形難以控制,因此產品精度高。
其缺點:
①由于該技術為“先焊接后成形”,焊接質量決定成形質量(傳統球罐是先成形后焊接) 。
②大型殼體成形過程支撐基礎難度大、費用高。